Today I took some inside-out pictures of this cotton blazer, and writing this post I have a sense of that summer refrain we all have heard or said - "are we there yet?" Yes, almost there with this jacket.
Last post I showed my collar seam pressing, so now it's time to sew the lapels.
Before I pin the lapel and collar seams, I usually mark the seam line at all the corners with a light pencil or chalk line. Hey - I am all about sewing things quickly and just one time. If I can precisely turn that corner on the lapel on the first go then that is great.
This picture above is slightly out of order as the upper collar has not been sewn on yet, but you can see where I have lightly marked the stitch line and corner angles with chalk.
Next the upper collar and lapels get sewn to the under collar and jacket body.
I divide this part into three sections where I pin and sew separately one lapel, then the collar part, then the 2nd lapel. No reason to pin the whole thing at once since the stitching stops at the inner corner. It just makes it easier to deal with to divide this into three manageable chunks.
If you would like to see another example of collar and lapel construction, this post from Jan 2011 showed some of these details when I made a winter wool coat for myself.
In the photo above are some of the many little squares created when I trim all the seam intersections. Depending on the garment it can look like fabric confetti around my work area. Trimming and pressing are two real keys to getting a tailored jacket to look right.
Speaking of pressing, I then press the entire seam allowance open on the lapel and collar. Sometimes I grade the seam allowances first and other times I press first and then grade, it depends on fabric. The thicker the fabric the more important it is to grade and eliminate the visible seam allowance outline that results from pressing an ungraded seam. There is a bit more about an interesting technique for seam grading in this post, scroll down to near the end.
The pressing tool I use to support that seam is the 5 position June Tailor pressing board, see below. I also have a sleeve board where the top part comes off and you can use various accessories that came with it, one of which is a long (20" or so) version of the pointy part shown in this photo below (which is about 8" or so. The long one is really great for pants or long seams in coats and jackets.
After those steps it is all pressed up and ready for the sleeves. I will wrap this up in two more posts so I can move on to other stuff. I have sewn a LOT of other things since I started writing this jacket series which I am ready to show. Including a very oddball bias stripe project that I started so I could write a Craftsy post, got involved in sewing an actual garment, started disliking it intensly and now have come around to being really happy with it, which I never would have predicted. (especially since I was trying to economize so purchased the fabric at the upholstery fabric outlet).
It actually rained today, for about 5 minutes, so weird for us in July. Not that it did my garden any good. For today's SunnyGal garden photo - these dianthus that are staying alive through winter and summer for about three years. Oh, how I love a nice little plant that persists.
Happy sewing, Beth
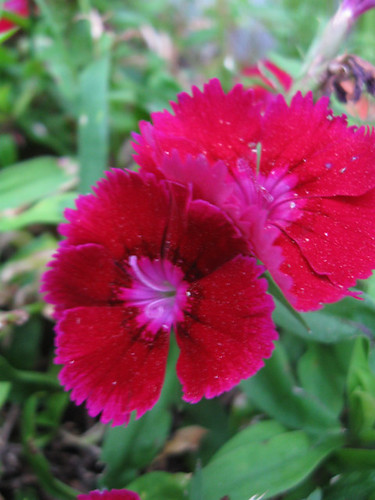
Am I correct that you left the seams raw in the pictures above? Is that ok for some fabrics?
ReplyDeleteThese jacket sewing posts are very interesting - especially, since I'll be attempting a similar, unlined jacket soon - although I'll be using a knit fabric.
:-) Chris
This has been really interesting - I'm looking forward to seeing the final jacket. Separately, I am just going to mention that I did reform my ironing-ways & have possessed a Muji compact full-height ironing board for a while now. (It's great for apartment dwellers). I think I need a press board now too…
ReplyDelete~Jen